Development of a Product Carbon Footprint Strategy
From planning to implementation
Due to the growing demands on sustainability and the need to comply with legal requirements, SMEs will also have to adapt their processes and strategies in future. A key step in this process is recording and measuring the CO2 emissions of a product over its entire life cycle (Product Carbon Footprint).
Merve Tuzcu is a Master's graduate in the Renewable Energies programme at the Faculty of Plant, Energy and Machine Systems at Cologne University of Applied Sciences. As part of her Master's thesis at Stannol GmbH & Co. KG, she has intensively analysed the topic of Product Carbon Footprint (PCF) and developed a PCF strategy for the company.

Practical approach
"Despite the increasing importance of PCF in industry, there are still only a few practical examples of the successful implementation of a comprehensive PCF strategy. While the theoretical foundations are well researched, there is a lack of concrete case studies that address the practical application and challenges of implementing PCF measures in companies," explains Merve Tuzcu.
This is where Tuzcu's work comes in: She examined the importance of the PCF using Stannol as an example and presented practical approaches for implementing and optimising the PCF. In addition, various scenarios were compared with each other, revealing the greatest influencing factors. By analysing CO2 emissions in detail, practical recommendations were also developed to help the company establish more sustainable business practices and improve its environmental footprint.
For business partners, the establishment of the PCF opens up the possibility of making informed purchasing decisions and favouring products with a lower environmental impact. In addition, the reported PCF can simplify and positively influence the calculation of one's own carbon footprint.
Challenges for SMEs
Many companies face considerable challenges when it comes to calculating their Product Carbon Footprint. One of the biggest hurdles are existing data gaps. Common databases often lack detailed information on certain materials or processes that are required for the calculations.
Another problem is the limited availability of specialised databases, which are necessary for calculating the PCF. Many SMEs do not have access to extensive and costly databases that provide comprehensive and up-to-date information. In addition, many companies, especially smaller ones, do not deal intensively with the topic of sustainability and climate accounting or are new to it.
"They often lack the expertise and human resources to cope with the complex requirements of PCF calculation. Without specialised experts, it is difficult for SMEs to determine accurate and reliable PCF data," says Tuzcu.
Detailed data collection
A decisive factor for a representative calculation of the PCF is the selection and use of suitable data. This in turn involves a great deal of time and labour, but is crucial for the quality of the calculation. At Stannol, both primary and secondary data were collected. The raw materials used could be determined promptly and precisely thanks to a good operational data collection.
In particular, detailed activity data was recorded for the most important production processes, such as the production of solder wire and solder pastes. This included electricity consumption, the use of chemicals and the use of materials.
As most of the emission factors could not be provided directly by the raw material suppliers, Stannol drew on established secondary databases, such as the information sheet on CO2 factors from the Federal Office of Economics and Export Control (BAFA) or the process-orientated basic database for environmental management instruments (ProBas).
If no data was available for certain raw materials, data for similar raw materials was used whenever possible to ensure appropriate comparability. For raw materials for which no specific data is available, the emission value of primary tin was used as a proxy. This approach is based on the assumption that the missing raw materials only account for a small proportion of Stannol's end products.
Calculation of CO2 equivalents
The activity data is converted into CO2 equivalents by multiplying it by the emission factors according to the formula below, which makes it possible to compare different greenhouse gases:
E = A * EF
E = Emissions in kg CO2 equivalents
A = Activity data in e.g kg, l, kWh
EF = Emission Factors in kg CO2 equivalents per unity
Cradle-to-gate approach
At Stannol, the PCF is calculated according to the cradle-to-gate approach. This means that the life cycle of a product is only considered up to the point at which it leaves the factory gate, i.e. from the cradle to the factory gate (see illustration). In concrete terms, this means that only the emissions generated in the phases of raw material extraction, production and transport of the raw materials through to delivery of the finished product are taken into account, while the phases of use and disposal of the product are not included.
"Cradle-to-gate is particularly relevant for intermediate products that are supplied to other companies for further processing. After leaving the factory gate, Stannol's products are used in many different downstream processes in industry (OEM and EMS) and by end users. In this case, it is therefore not possible to trace and determine the value in the context of the subsequent life cycle without additional resources," explains Merve Tuzcu.
Secondary materials offer the greatest savings potential
The calculations carried out by Merve Tuzcu make it clear that at Stannol, both the switch to secondary materials and the use of renewable energy sources enable savings in the PCF. However, the extent of the reduction in emissions varies depending on the product category and composition of the materials.
"A key finding is the major influence of the choice of materials, especially for products containing tin and silver. The use of secondary materials leads to a significant reduction in emissions here, as silver and tin are major sources of emissions. Switching from conventional to renewable electricity also reduces emissions, but to a lesser extent, as the majority of emissions come from metal production itself," explains the Master's graduate.
82 percent savings for products containing tin and silver
The product categories with the highest savings potential, such as solid solder wires with a high tin and silver content, show the greatest reductions, particularly with the use of secondary materials and renewable electricity. Emissions could be reduced by up to 82 percent here. Fluxes, on the other hand, show a lower reduction potential due to their chemical composition, although renewable energy sources also have a positive influence here.
"The results of this work show that the reduction of PCF can be significantly influenced not only by technical optimisations in production, but also by the conscious selection and combination of the materials used. In particular, the increased use of secondary materials and the utilisation of renewable energies have proven to be effective measures for reducing overall emissions," explains Merve Tuzcu. These strategies not only help to reduce CO2 emissions, but also promote resource conservation, which is increasingly in line with regulatory requirements and market expectations.
Further potential for savings comes from packaging, which is a constant source of emissions for all products. Packaging should therefore also be considered in future measures to reduce emissions in order to further improve the carbon footprint of products.
Recommendations for the future
The installation of a PV system, in addition to the purchase of certified green energy, can contribute to a considerable reduction in emissions in the long term and reduce dependence on fossil fuels. Increased cooperation with recycling companies and the development of a sustainable procurement strategy could support this measure. In addition to tin, the use of other recycled materials also offers potential for reducing emissions.
"In order to achieve their own sustainability goals, suppliers should also be more closely integrated into the sustainability strategy. By defining clear standards and expectations with regard toCO2 emissions as well as regular reporting along the supply chain, upstream emissions can also be better controlled and reduced. This could be incentivised through preferential supplier relationships or long-term contracts," recommends Merve Tuzcu.
Author
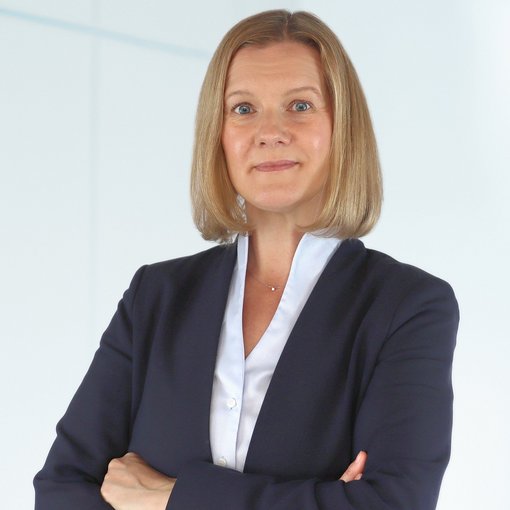