Flowtin Soldering Extends Solder Nozzle Service Life
The service life of soldering nozzles is an issue in every soldering company. The problem is that the soldering nozzles wear out over time during the soldering process. This, in turn, has a negative influence on the even flow of the solder over the nozzles, which worsens the soldering result. For this reason, the soldering nozzles must be changed regularly. However, each change results in increased costs, time, production interruptions and personnel.
RAFI GmbH & Co. KG, based in Berg near Ravensburg, Germany, has been using Stannol’s patented Flowtin solders on its selective soldering systems for some time and found that the solder nozzle service life has been significantly extended with the help of Flowtin. Romano Reising, process technologist at RAFI, accompanied the conversion of the systems.
Micro-alloying ensures lower dissolution
The micro-alloyed flowtin solders were developed in the Stannol research and development department by Dr Werner Kruppa. They are particularly suitable for production areas in which the lowest possible alloying (leaching, erosion) of copper and iron plays a key role in a stable soldering process. "Due to the low addition of cobalt and nickel, these solders have a lower copper and iron solubility, which leads to significantly longer service lives of the solder baths,” explains Dr. Sven Mönninghoff, Head of the R&D Department at Stannol. “However, Flowtin solders have another positive effect: the service life of the soldering nozzles used can also be extended with the help of the micro-alloyed solders, as tests at the customer’s site show.”

Testing Flowtin
At RAFI, the previously used solder Ecoloy TSC305 was replaced by Flowtin TSC305, all other parameters remained the same. Flowtin TSC305 (Sn96.5Ag3Cu0.5) is a lead-free solder analogue to ISO 9453 (alloy no. 711). "We first compiled relevant data, such as the service life of the nozzles used before the change, in order to ensure comparability. Standard nozzles in various sizes were tested until they showed defects. A crucible was then filled with Flowtin TSC305 and the change of nozzles used was documented over four months in three-shift operation," said Reising.

Maintenance Interval Significantly Extended
The result is that the service life of the nozzles was doubled with the help of Flowtin. “The regular running time of the 4.8 mm nozzles was about 60-65 hours before the change. After switching to Flowtin, we now achieve service lives of up to 130 hours,” said Reising, who was positively surprised by the result. “I had expected an extended service life of the nozzles of about 20-30 percent; however, the actual result far exceeded my expectations." Even with the smaller and very sensitive 2.5 or 3.6 mm nozzles, RAFI still achieves an extended service life of around 60-70 percent. However, the exact durability of the nozzles also depends on the material to be processed, the selected soldering process, the machine parameters, and the maintenance and care of the nozzles – individual deviations may occur.

Significant Cost, Time and Personnel Reductions
After the successful four-month test phase, a second selective soldering system at RAFI was completely converted to Flowtin, and after a further six months, all remaining systems – including those at the RAFI site in Hungary – were successively converted. In total, Flowtin is now in use at RAFI in five selective soldering systems with several solder crucibles.
“The changeover to Flowtin went quickly and without any problems. The biggest advantage for us is the enormous cost savings, as the price-intensive soldering nozzles have to be changed much less frequently. Longer change intervals also save time and ensure that production is interrupted less frequently,” emphasized Reising.
It can be assumed that the micro-alloyed Flowtin solders also have a positive effect on the durability of the riser tubes and crucibles, as the coatings are less attacked overall. “However, this effect can only be assessed precisely in one to two years because then the first signs of wear on the riser pipe usually appear. Based on previous experience, I suspect that there will also be positive effects on the service life in this area,” explains Reising.
About RAFI GmbH & Co. KG
- RAFI in Berg near Ravensburg is a technology leader and innovation driver in the field of industrial man-machine communication.
- RAFI's portfolio includes control and signalling devices, micro switches, electronic assemblies, touchscreens, joysticks and digital solutions.
- Founded in 1900, the company now has around 2,500 employees at eight locations in Germany, Europe, China and the USA.
Stannol Flowtin Solder
- finer-grained and smoother surface than conventional SnAgCu alloys
- reduced dissolution rate – significantly longer service life of the solder baths
- gentle on soldering nozzles – lower cost, material, time and personnel
- also available with reduced silver or silver-free for high cost efficiency
- all Flowtin solders are available as a sustainable greenconnect version (significant CO2 savings)
Author
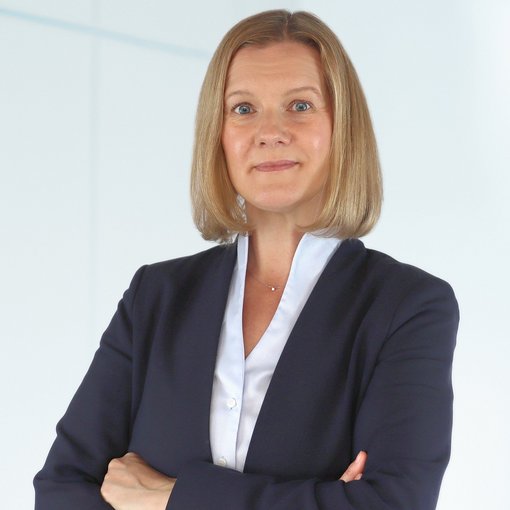