Kolb Fertigungstechnik relies on greenconnect
W. Kolb Fertigungstechnik GmbH has already been a permanent member of Stannol's customer base since 2019. The Willich-based company with around 180 employees has been manufacturing electronic assemblies for customers from a wide range of industries for around 30 years. In spring 2022, Kolb switched its entire THT production to Stannol's sustainable greenconnect range. Mike Prince works in production engineering at Kolb. In this interview, he explains how the change from conventional solders to greenconnect solders and fluxes worked out.
How did you hear about greenconnect?
M. Prince: Quite classically via our contact at Stannol, who introduced us to the products and was able to inspire us straight away. At that time, we had already been dealing with the topic of sustainability for some time and had asked ourselves how we could reduce our carbon footprint, for example. Stannol's greenconnect products were therefore a good starting point for us.
Why did you decide to switch to greenconnect? What do you expect from the change?
M. Prince: Our plan is to use materials in the future whose manufacture applies sustainability principles that go beyond the legal minimum. For us, this means, among other things, using resources responsibly and in moderation, avoiding waste and minimising our carbon footprint. But the origin of the raw materials we use is also important to us. Tin mining in particular is characterised by child labour, a poor level of occupational safety and a massive lack of transparency. We therefore see it as our social responsibility to support fair tin mining – and to use products that guarantee a compatible approach to people and the environment.
Which greenconnect products do you use specifically?
M. Prince: We started at the end of 2021 with the Fairtin Kristall 611 solder wire, which we use for hand soldering. We were convinced not only by the fair origin of the solder, but also by its high quality: flux spitting is extremely minimised with Kristall 611, which leads to very good soldering results. We then decided to switch our entire production to greenconnect in order to exploit the full sustainability potential for ourselves. Fairtin solid solder wire for our selective soldering system and Fairtin solder bars for the wave soldering system followed. Then, in March 2022, the EF350 Bio flux was added to complete the package.
How did the changeover work out in production?
M. Prince: It worked smoothly, the products convinced us right from the start. The composition of the EF 350 Bio flux, for example, is almost identical to that of the conventional flux. We were therefore able to simply replace the flux – without having to change the process parameters. We did carry out a test run in advance as a precaution, but there were no real concerns during the change. After all, the experience we have had so far with Stannol products has been consistently positive. Added to this is the trusting and reliable cooperation with the sales department over many years.
Author
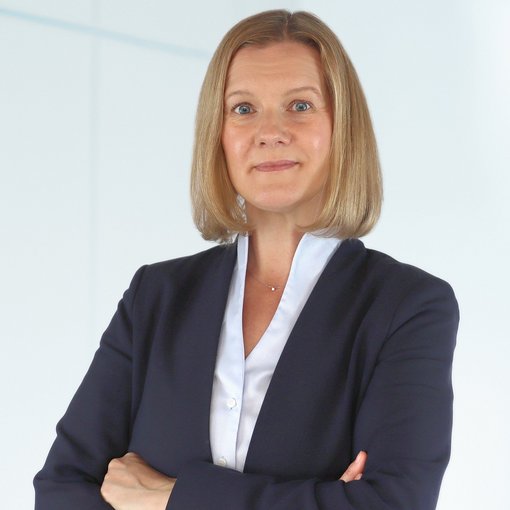