Minimise soldering defects, save costs
Soldering defects that occur during the production of printed circuit boards can have serious consequences - from costly reworking to unusable rejects to the complete failure of the manufactured electronic assembly. To avoid this, the solderability of PCBs or the metallic connections of a component should be tested in advance. Solderability tests using wetting balances can provide reliable support.
The assembly of PCBs is becoming increasingly complex: PCBs and components are becoming smaller and smaller, while the density of components is rising. At the same time, weaker activated fluxes are used for the filigree assembled surfaces, as these are more mildly formulated. However, this increasingly reduces the process window for the soldering process, while poor solderability can result in costly consequences. "Although known components with good solderability are usually chosen for components and PCBs, this cannot be guaranteed without testing.
This is mainly because uncontrolled storage and the age of the components are the main causes of poor solderability," explains Nicolas Wiacker, product manager at Stannol.
Longer storage times, including those caused by interrupted supply chains or long transport distances, can contribute to the oxidation of component surfaces, which can lead to limited solderability. Solderability tests can be used to reliably determine in advance whether conductors on PCB surfaces or component connections show consistently good solderability and whether they can withstand the demands of assembly processes. This minimises the risks of soldering defects in production.
Wetting Balance Test: physical principles
The most meaningful method for measuring, testing and recording solderability is the wetting balance test. This makes use of the physical principles of weight and speed. When a metallic body is immersed in a solder bath, the weight and speed with which the solder meniscus rises at the immersed surface indicate how well the body is wetted by the solder. The weight and speed thus represent a measure of its solderability. This can be measured by the vertical force acting on the suspended specimen. This means that the higher the solder meniscus rises at the surface, the better the solderability.
Wetting Balance Test: procedure
If the solderability of a PCB or a component is to be tested by wetting balance, a test section of the PCB or a corresponding test plate is first removed for this purpose. In the case of wired components, a standard flux is then applied to the component lead or to the area to be tested and dried. The test specimen is then clamped into a component holder of the wetting balance while the solder bath is raised at a predetermined speed. The test specimen is then immersed to a preset depth in the oxide-free bath of molten solder, the temperature of which is kept stable by a temperature controller.
Sensitive measurement process
The wetting balance now measures the course of the vertical force acting on the test specimen over time. Changes in the forces during wetting are then converted into digital signals at a high measuring rate of 1,000 Hz. This data is automatically acquired, stored and evaluated by the associated software. The result is a force-time curve (wetting curve) from which the solderability of the test specimen can be objectively determined. "During this process, there must be no vibrations whatsoever, otherwise the test result could be falsified," emphasises Nicolas Wiacker. "It is best to place the wetting balance on a vibration-decoupled surface to minimise measurement errors." Regular calibration of the sensitive devices is also essential to achieve accurate measurement results.
The greater the wetting force, the better the solderability
A typical wetting curve initially drops. This is due to the buoyancy force that the molten solder exerts on the test specimen. This effect continues until the specimen is warm enough to be wetted by the solder and the flux begins to act.
With small specimens, this happens relatively quickly and can begin as soon as the specimen is immersed in the solder bath. Subsequently, the curve and solder meniscus begin to rise.
The speed of this process is determined by how well the flux cleans the surface of the specimen. When the solder meniscus stops rising, the wetting curve flattens and approaches its maximum value. The force applied at this point is called the wetting force: The greater the wetting force, the better the solderability of the component.
"The time taken to reach the maximum force or wettability then determines the suitability of the test specimen for the soldering process used and the production speed," explains the expert.
Micro-Wetting Globule Test for small components
The testing of particularly small components, connections or multi-pole components is made possible by the so-called Micro-Wetting Globule Test. Here, the solder bath is replaced by a block of solder globules of different sizes, for which solder pellets of different weights can be used – depending on the size of the test specimen. In this way, a greater wetting force can be obtained for evaluation.
With this method, too, flux is first applied to the test specimen and dried, and the specimen is attached to the measuring head of the wetting balance. Nicolas Wiacker: "Depending on the globules used, we place a 5, 25, 100 or 200 mg solder pellet on a thermally stable heated globule carrier in our device. As soon as the solder globule wets the component connection, it is pulled down by the surface tension of the bridge of molten solder that forms between the globule block carrier and the test specimen." The wetting curve and solderability are then likewise determined from the measurement of the force over the measurement period.
"Step & Repeat" Function
The solderability test system used at Stannol also offers a "step & repeat" function for multi-pole components. This means that several contacts of a component can be tested in series one after the other. This not only saves time, it also ensures that the individual contacts are tested under the exact same conditions. "The "step & repeat" method was developed specifically with regard to the more stringent testing requirements for the current miniature SMD designs," explains Nicolas Wiacker.
Easy change to organic fluxes
Another area of application for the wetting balance is the testing of fluxes. With the help of the measuring device, it is easy to find out whether or how a soldering result changes when the flux is replaced - under otherwise identical conditions. "For example, it is possible to check whether a flux used can be replaced by a bio-flux, without having to make time-consuming changes to the process parameters during operation," says Wiacker.
Testing according to customer specifications
Stannol tests material samples for its customers to ensure that the respective components show good solderability. "How much is actually tested depends on the customer. The larger the test quantity, the more representative the result in the end. As a rule, about 10 to 15 test specimens are useful," explains the expert. Tests are carried out according to predefined standards such as J-STD-002 or according to customer-specific requirements. The orientation of the component (immersion angle), the brazing temperature, the alloy, the flux used, and the immersion depth or speed of the test specimen are all specified.
Standard components are often tested according to the standard, while customer-specific components may also deviate from the standardised test parameters. For this purpose, the test parameters are precisely defined in advance with the customer. Nicolas Wiacker: "For some components, it is necessary to change the test parameters of the standard because they are not suitable for certain components – for example, if a larger component dissipates heat very strongly. In such a case, the standard settings make little sense and should be adjusted accordingly."
As a rule, solderability tests according to the standard take place under conditions that are more difficult than in real production. This is because in production, the process conditions can be influenced in such a way that the soldering process is additionally supported – for example by preheating or the use of inert gas. For this reason, it is possible that a component that does not perform well in the solderability test may still be considered for production. However, this cannot be guaranteed. If a test specimen fails the test, i.e. if the solderability is proven to be poor, the corresponding component batch is usually discarded.
Nicolas Wiacker: "The process windows are usually so small that it is not possible to change the production parameters in such a way that good solderability is achieved in the end. Therefore, the components are then usually not used." This also applies when there are extreme differences in the test results. If one half of the test specimens shows good solderability, but the other half shows poor solderability, there is a high risk that problems will arise later in production. All results are recorded in a detailed test report.
Testing of recycled components
Since the beginning of the Corona pandemic, many electronics manufacturers have been struggling with supply bottlenecks for electronic components. It was not uncommon for production to continue only to a limited extent or even to come to a complete standstill. Since then, many manufacturers have increasingly turned to other sources to procure components, for example components from professional recycling companies. "In addition to the function, it is also imperative here to check with the help of solderability tests whether the components are still sufficiently solderable after re-tinning. Especially because you don't know what life cycle the component has already gone through," the expert emphasises.
Solderability tests can contribute significantly to improving product quality and to high savings because they reduce defect rates in soldering processes. Another advantage: "The tests can facilitate the use of milder No-Clean products and environmentally friendly soldering materials – especially with regard to sustainable production, these are aspects that should not be neglected."
The MUST System 3 tests according to the following standards:
- IEC 60068-2-54 and 60068-2-69 (2-54)
- MIL-STD-883 PROCEDURE 2022
- IPC/EIA J-STD-003A
- IPC/EIA/JEDEC J-STD-002E
- EIA /JET-7401
Contact our Expert
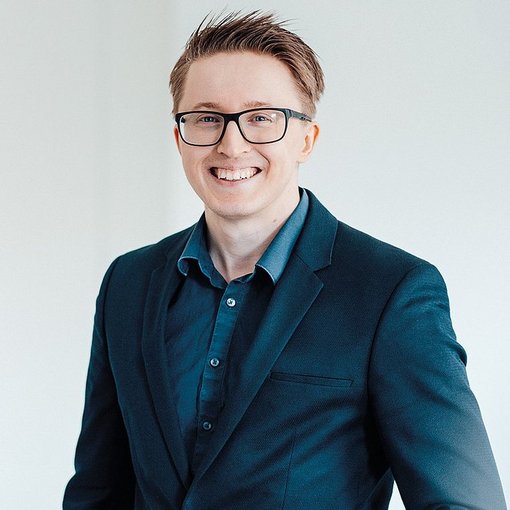
Author
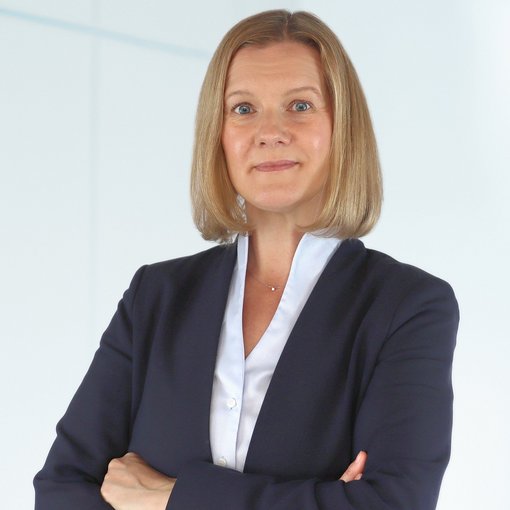